The different elements that make up an alloy can drastically change the mechanical properties, corrosion resistance and the metal’s microstructure. While chromium, nickel, molybdenum, iron may be the primary alloying elements, other elements like tungsten, carbon, aluminum, titanium, copper and sulfur can have significant effects as well. Understanding the elements and both positive and negative effects on the alloys can help to identify what applications certain alloys can be used in.
Nickel (Ni)
Improves high temperature strength, resistance to oxidation, nitridation, carburization and halogenation. It also provide metallurgical stability. Presence of this element can improve resistance to reducing acids and caustic and resistance to stress corrosion cracking.
Chromium (Cr)
Alloying with Cr improves resistance to higher temperature oxidizing and sulfidation and resistance to oxidizing environments in general. Such oxidizing media include both nitric and chromic acids. Additions are typically in the 15 to 30% range but has been seen as high as 50%.
Molybdenum (Mo)
The addition of molybdenum significantly improves the resistance to non-oxidizing acids such as, hydrochloric (HCl), phosphoric (H3PO4) and hydrofluoric acid (HF). It has also been shown to be used to improve resistance in sulfuric acids (H2SO4) in concentrations below 60%. Mo improves resistance against pitting and crevice corrosion and imparts high temperature strength.
Iron (Fe)
This element reduces the cost of the alloy and improves high temperature carburizing resistance and controls thermal expansion.
Tungsten (W)
This element is similar to Mo in that it provides resistance to reducing acids and localized corrosion and imparts enhanced strength and weldability.
Carbon (C)
Can hinder corrosion resistance but adds strength at elevated temperatures.
Aluminum (Al)
Additions of Al can promote the formation of a tightly adherent alumina scale at high temperature that resists attack by oxidation, carburization and chlorination. In combination with Ti, it also promotes age hardening in certain alloys.
Titanium (Ti)
As mentioned above, it promotes age hardening, and can also combine with carbon to reduce susceptibility to intergranular corrosion because of the chromium carbide that forms after heat treatment.
Copper (Cu)
Improves resistance to reducing acids. Alloys that contain 30 to 40% Cu offer excellent resistance to all concentrations of non-aerated HF. If Cu is added to a Ni-Cr-Mo-Fe alloy, resistance to hydrochloric, phosphoric and some concentrations of sulfuric acids is improved.
Cobalt (Co)
Cobalt imparts unique strengthening characteristics to high temperature alloys. Cobalt also increases the resistance in nickel alloys to carburization and sulfidation. This is due to the fact that Co increases the solubility of C in Ni base alloys and because the melting point of cobalt sulfide is higher than nickel sulfides, respectively.
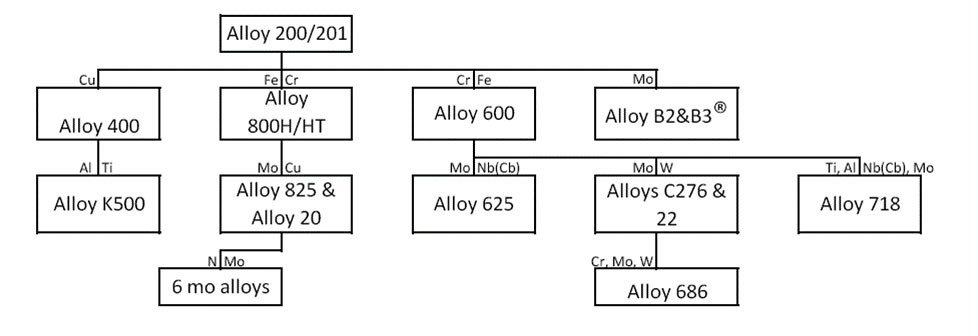
Post time: Dec-19-2022